Making An Elite Cooler
What does it take to make a Pelican Elite Cooler? Well, there needs to be lots of insulation to provide extreme ice retention. But the insulation needs to go somewhere. Best bet is in-between the durable plastic walls of the cooler. So what is the best way to actually go about making those walls? It is time to consider rotomolding vs. injection molding coolers.
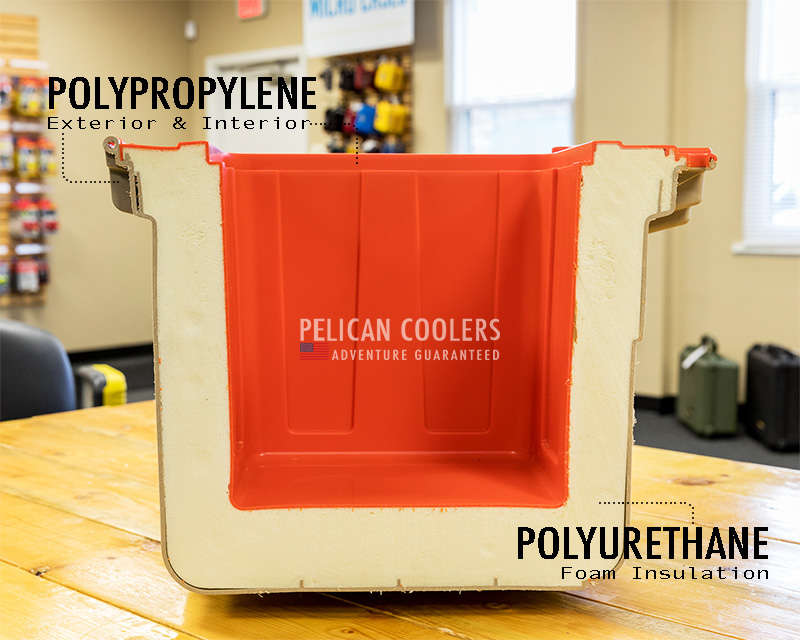
The Gold Standard
Rotomolding, a shortened form of rotational molding, has long been the industry standard for high-end coolers. This manufacturing process results in thick, even walls, particularly in the corners, which provides great strength against stress. The first generation Elite Coolers (known at the time as the ProGear Elite Coolers) were all rotomolded. These coolers had incredible durability thanks to the rotomolding process and incredible ice retention thanks to the 2" of polyurethane foam insulation. Today the Elite Wheeled Coolers—along with the massive 95QT, 150QT, and 250QT Elite Coolers—are still rotomolded. Unfortunately, rotomolded coolers are heavy because of those thick plastic walls and all that insulation. Even an empty rotomolded cooler can be a chore to move around.
Injection molding uses less plastic, so the end product is lighter, up to 30% lighter than comparably sized rotomolded coolers! Injection molding can also accommodate more complex designs, like the ridges and fins that add extra durability to the injection molded coolers. Injection molding can’t be used to create hollow products, so instead an interior wall and an exterior wall must be created and then fitted together before being filled with polyurethane insulation. Pelican turned this into a bold design feature, creating dual-toned coolers featuring a bold exterior with a contrasting interior. Of course there is still a 2" layer of polyurethane foam insulation in the injection molded coolers, so they can deliver the same extreme ice retention that a rotomolded cooler would.
Rotomolding vs. Injection Molding: FIGHT
Every manufacturing method has its pros and cons, which often impact which method is chosen. So let's get into the nitty gritty to figure out the advantages and disadvantages of rotomolding vs. injection molding coolers.
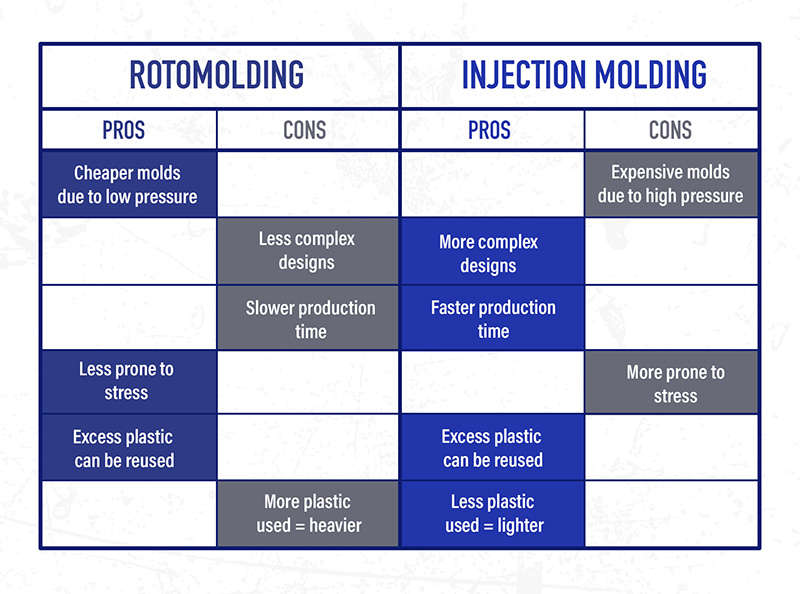
Cost: Initial cost is a huge consideration when it comes to manufacturing. Thanks to the low pressure way in which rotomolding is done, less expensive materials can be used to create the molds. Injection molding requires high pressure, and therefore stronger (and more expensive) molds. Rotomolding wins this round!
Design complexity: Both of these methods can be used for all sorts of designs. Injection molding just edges out ahead of rotomolding because of the high pressure that ensures plastic fills every nook and cranny in the mold. Injection molding wins this round!
Production time: Costs can be offset if products are able to be produced and sold more quickly. Injection molding is quick thanks to the high pressure used. Rotomolding just takes longer for each piece. Injection molding wins this round!
Manufacturing stress: During the molding process high stress can cause discoloration in the plastic or other stress marks. Thanks to the low pressure needed for rotomolding, these types of stress marks almost never happen. Rotomolding wins this round!
Waste: When thinking about waste in response to the question of rotomolding vs. injection molding coolers, the good news is that waste is limited in both methods. Excess plastic, often called flashing, can be removed from the product and used again in the creation of another product. This round is a draw!
Weight: As outlined above, rotomolding uses more plastic and results in a heavier product than injection molding does. This round goes to injection molding!
And the Winner is . . .
Injection molding comes out on top after six rounds of rotomolding vs. injection molding. But it is a close match and rotomolding still provides excellent results in a high-end cooler. So for Pelican the answer to rotomolding vs. injection molding coolers is: BOTH! It just depends on the needs of each particular cooler. Plus, no matter which method Pelican uses to make their Elite Coolers, they back the coolers up with an unmatched lifetime warranty. And all hard-sided Pelican Elite Coolers are proudly made in America.